Deck Foundations – Everything you need to know before you dig.
One of the most important aspects of designing a deck has nothing to do with what we see. Most decks have a foundation underground that has to be considered and engineered for the specific soils and deck size. Things can get difficult; large boulders and rocks are not uncommon. It is also important to consider buried septic tanks, propane tanks, and utilities before digging. We have even found buried tree stumps and a slabs of concrete that offered unexpected challenges to the foundation construction.
Types of Deck Foundations
This blog isn’t about to dive into every option, but here are some types of foundations we know about and we have used most of these. In fact, most are good options depending on the situation.
Non-Frost Rated Foundations
These can be used for a few types of structures but cannot be used for a structure that is attached to a another structure. The frost heaving will affect structures on these foundations. If one structure is moving with the frost and the other is not, each structure could be damaged by those stresses. Some options for non-frost rated foundations are:
- Pinning to flat rocks
- Concrete blocks
- Small helical piles and other small ground screws
- Ground spikes
- Plastic blocks
- Shallow posts (concrete, wood, or metal)
Frost Rated Foundations
These are your deeper foundations. Here in New Hampshire we are talking 4’+ depth. In reality your frost depth in coastal regions is far less than inland, but for the most part New Hampshire towns have a one-size-fits-all approach. Well, maybe two sizes. The colder it is, up in the mountains and further north, the deeper the foundation has to be. Here are some frost-rated foundations:
- The most common is poured concrete often in cylindrical forms and often reinforced with rebar or other products. Very heavy and labor intensive. Can be engineered and built in-place as a post higher than many other solutions.
- Helical piles are a very solid product. They are light-weight but take a particular tool and expertise to install. Affordable but not something you can do yourself. Huge benefit is the engineering report that shows compaction and thus bearing strength of the earth. Steel posts can support beams a few feet above ground without additional post.
- Pre-cast concrete piers; very high quality but very heavy. Requires heavy equipment to transport and install. There is a sectional product which reduces the weight of each section to… still a lot. Terminates at ground level connecting to a post.
- Pinned blocks use large pins driven at various angles. Quick to drive, not as easy to back out.
- Sunken wood post. A rot-resistant or treated wood installed directly in the ground often on a footing. Footing materials can vary including rock, concrete, wood, and plastic. One post spanning from frost-depth to the deck.
Of all these options the most versatile is sunken wood post. Hole, wood, done. The poured concrete option has downsides, including production and quality assurance problems. Poured concrete piers can go do any depth but the excavation for deeper pours goes up exponentially. Pre-cast concrete has the same excavation issues but isn’t sectioned into 80lb-just-add-water bags, meaning you can’t move it without heavy equipment. Helical piles can go as deep as needed by the same machine using extensions. A huge benefit to helical piles is that you (might) not have to dig, meaning you do not disturb much soil. The pinned blocks also do not disturb soil, potentially, but might hit obstacles that result in excavation anyway (as any foundation can, but with 4 pins at diagonal angles…) And so the winner right now is sunken wood posts on plastic footings. Straight-forward, accessible, light-weight, just dig a hole, no water needed, plastic footings are cheap. You can weatherproofing the ground level area extra but the goal with wood is keep water and oxygen away. When those two combine in a prolonged setting the rot can flourish and your post will decay quicker, though by all means not over night or over even a few years.
Obstacles
Underground Utilities
After a great deal of planning (the deck layout is set, the plans are approved, and you have a permit in hand), it is time to install your foundation right? Well, not quite. When it comes to utilities homeowners usually know where their septic and propane tanks are buried, but in places with municipal utilities it may be harder to know. Damaging a utility line can be dangerous and costly. Fortunately, we have Dig Safe, a simple website to request utility lines be marked. Dig Safe contacts the utility companies to come out and mark the ground where their lines are buried. Here’s what you need to know:
- Mark the area you are going to dig with stakes, flags, or paint. This can be done by you or your contractor. Try to be as accurate as possible. If you are off more than 18” you will need to remark the area and reschedule with Dig Safe.
- Contact Dig Safe 72 business hours before you are ready to dig. Dig Safe will notify your utility companies and within 72 hours they will mark will mark any buried utilities in your project area.
- Go to http://www.digsafe.com/ for more information about orders, mark meanings, laws, and more.
Boulders, Rocks, and Granite Shelves
So, now that you have your utilities marked it’s really time to dig. If this is a small DIY deck project and you don’t have large digging equipment, not to worry. It is possible to dig all your foundations by hand-shovel. We had one particular project in the summer of 2020 where we dug all 9 piers by hand. Most of them were not a problem, but there were three areas where we hit very large rocks. Since the foundation layout is very particular, moving a pier somewhere else to avoid a large rock wasn’t an option. And since the building inspector wanted to see that the holes were at least 48” deep we had no other choice but to get those large rocks out. Here’s what to do with a tough rock in the way:
- Dig around the rock until you see the edges. This may mean digging a bigger hole than you planned. Keep opening up the area around the rock until it is very exposed. Sometimes this is enough to get it out.
- Change up your tools. Shovels are great for just digging, but make sure you have a pick axe and bar on hand. A bar can be used to get into small spaces, chip away at the rocks, and loosen and dislodge some of the larger debris. Here is a crazy idea: we sometimes use a shop vacuum to get hard-to-reach sand out from under the boulder, which often lets you dislodge the whole thing.
- As you loosen the large rock, start to leverage wood boards, branches, or whatever you have on hand under the rock. Continue to pry up the rock and shove items under it until you work the rock out, usually in a back and forth method (leverage one side up, slide board under. leverage other side up, slide board under). We used several boards under the boulders until we could get them out.
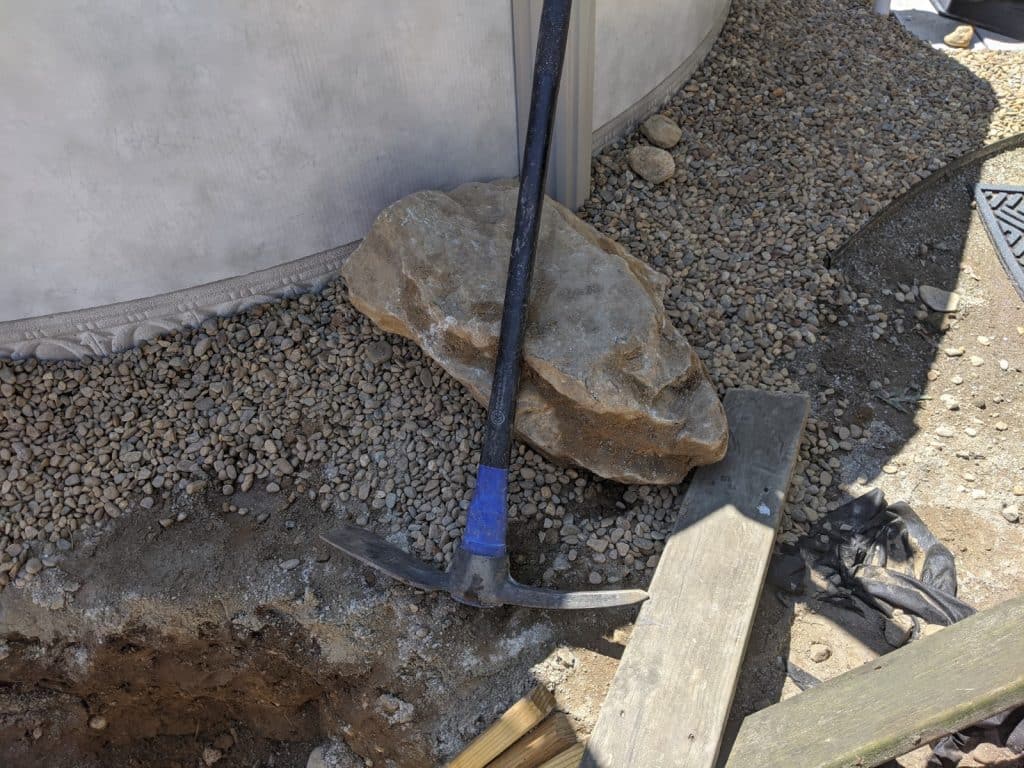
But what happens if that boulder never ends? If you keep digging and digging to realize that you may actually be on top of a granite shelf? Here’s what to do:
- Give it your best effort. Make sure you dig as much as you can around the rock to verify that it truly isn’t coming out.
- Call your building inspector. Explain the situation to the building inspector and verify that he/she will approve of you bolting the foundation to the granite shelf or boulder. Likely, they will want to inspect the hole and the boulder before approving this.
- Anchoring your foundation to a boulder with a pin usually involved drilling a hole in the boulder, and hammering in a bolt or piece of rebar. However, the details depend on your project. Discuss your methods and materials with your building inspector or engineer.
Winter
Autumn is when we race against the clock to install foundations before the ground freezes. With heavier equipment ground freeze doesn’t need to be a hindrance, but if you are digging your foundation by hand-tools, make sure they are in before it’s too cold. Even though we have some larger digging equipment, we still prefer to install our foundations before too much ice and snow accumulates. We use the Fall to schedule foundation installs for multiple project. Once the foundations are in we can go back at any time in the winter to complete the rest of the deck project.
Ground Water
We recently completed a deck on a property with a high water table. The holes kept partially filling up with water, making it difficult to pour concrete for our piers. So, after informing the building inspector, we installed pre-cast concrete piers. The piers weigh hundreds of pounds so we had to move them with our F-350 and our Bobcat. We used 2×4 lumber to control the pier as we set it on a base of compacted stone.
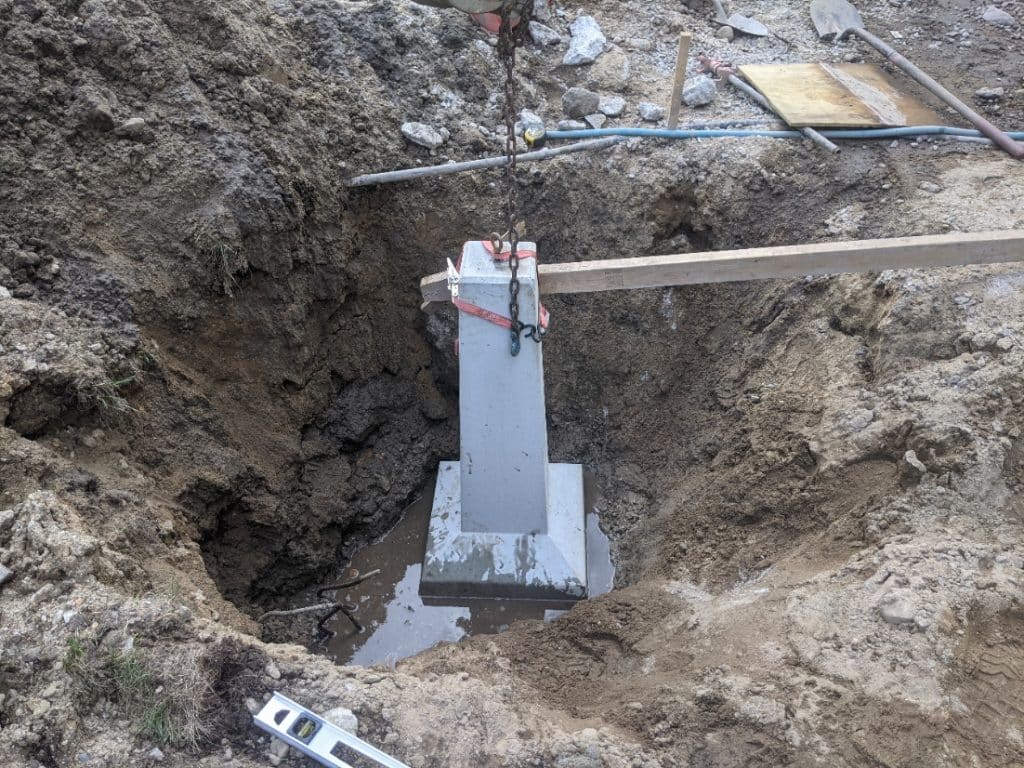
Random Things in the Ground
Sometimes you don’t know what you are going to find underground until you start digging. On a recent deck project we encountered a couple of massive boulders that matched those used for the backyard retaining wall. It looked like these two boulders were two too many and the builders ended up burying them. On this same project we also unearthed huge patches of buried concrete. During the home construction the excess concrete needed to go somewhere and it looks like the builders decided to bury it in the backyard. Needless to say, this simple foundation install became a very complicated process. Even with our heavy digging equipment we were way over the original estimated time to install. For this reason, our contracts often give our best estimate for foundation installation, but the charges will be calculated off of the actual time and materials costs.
If you are hiring a professional or building a deck yourself, be sure to consider the many unseen factors that affect foundation installation. Weather, ground conditions, and utilities can effect the layout, materials, scheduling, and cost of your deck.